The Build-Before-Design Approach to Large Equipment:
Why It’ll Save You Time, Money, and Headaches
Product Insight has developed a wide range of large-scale products over the years. Sweating the Small Stuff in Big Equipment is our series on the unique challenges of producing large equipment. We’ll discuss usability, design, and manufacturing issues while sharing best practices for meeting these challenges.
Product Insight specializes in large equipment that supports life-changing work like conducting cutting-edge research, building society’s technological infrastructure, and curing inoperable cancers. But even big machines must be easy to use and service. They need the kind of good design you know by sight, touch, and feel. And you can’t duplicate those sensations virtually.
The best way to understand how individuals might use a product is to actually start using it. That’s why simple mock-ups and physical prototyping are essential to a successful design process.
While quick, iterative model making is commonplace for smaller products, the sheer scale and complexity of large equipment mean that this part of the process is often skipped. Yet our experience shows that rapid prototyping is even more critical for large-scale equipment because the risks can be so great. These machines present unique and challenging issues for human interaction. And with their high production costs, reworking mistakes can quickly get very expensive.
One industry leader in the semiconductor field learned this the hard way.
The Case of the Seven-Foot Cube
This company makes large, highly specialized industrial machinery used by workers all over the world in factories manufacturing and testing semiconductor chips. By the time they engaged with Product Insight to help them bring their latest model to market, they had already invested years of R&D and engineering effort to develop the core technology and internals. Any changes were assumed to be mainly cosmetic. Just to make sure, the PI team built a simple, full-scale mock-up to understand how a typical user might interact with the finished device.
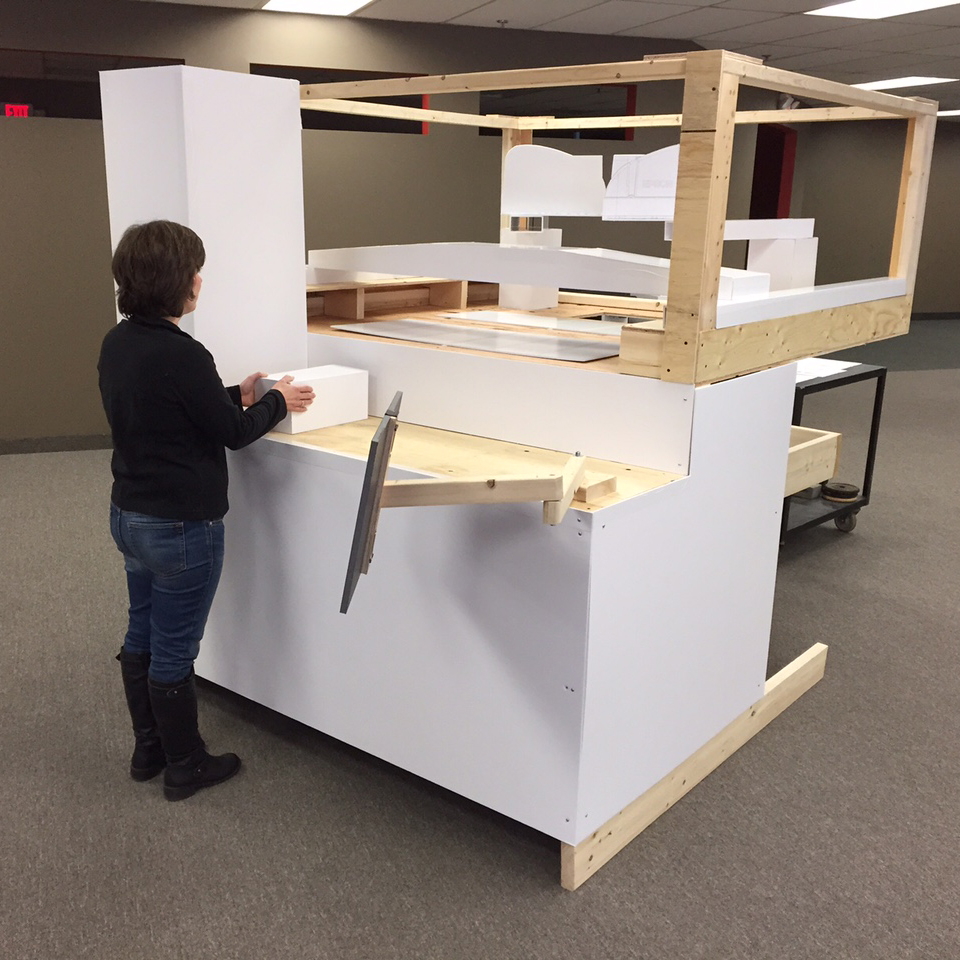
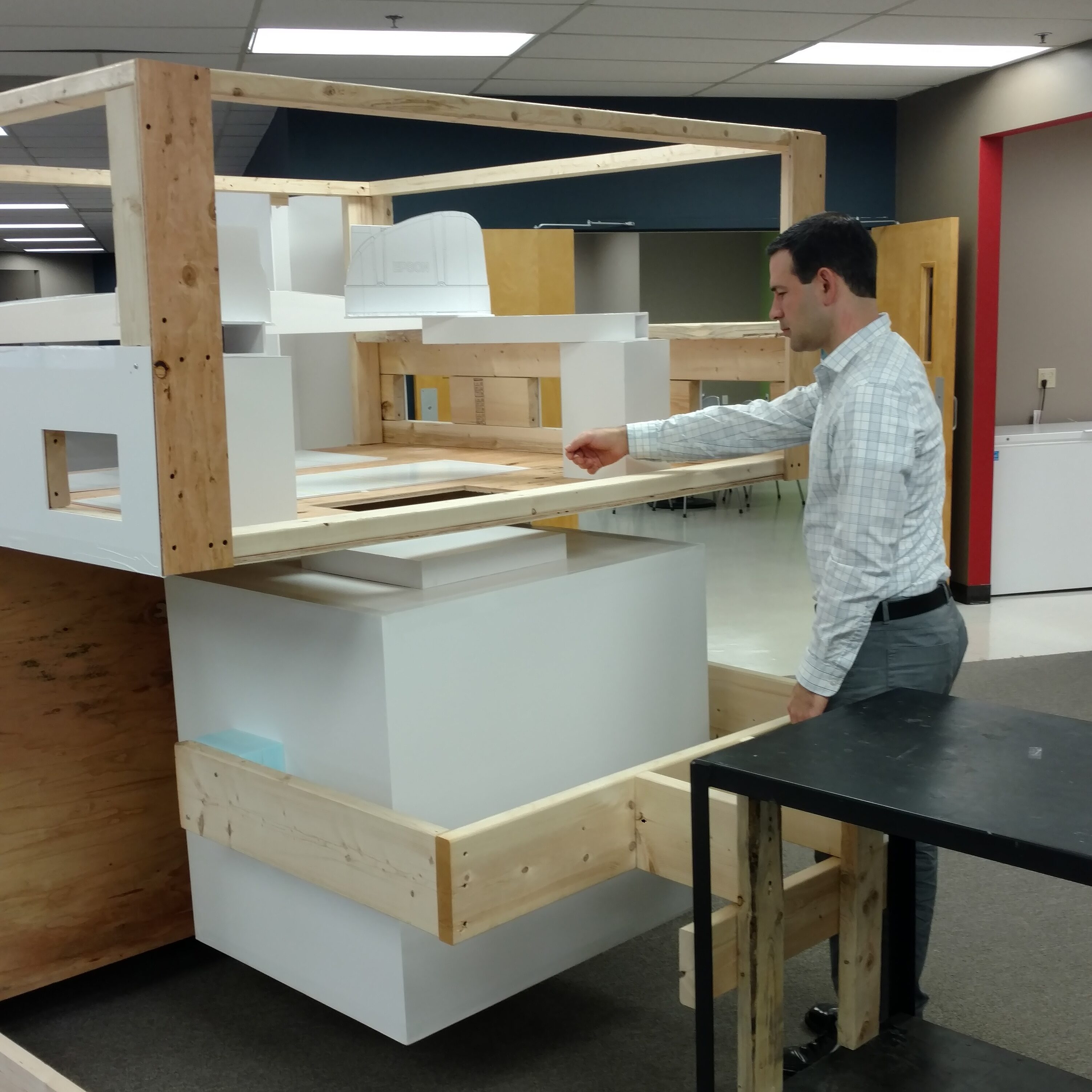
We were all shocked at the sight of a seven-foot cube. Usability issues were immediately clear just from looking at this simple wooden model: workers could not reach critical access points for regular maintenance or adjustments—at least without a stepladder.
The good news was that this discovery was made early enough that it didn’t completely derail the program. Others have not been so lucky.
This company learned three important lessons about the importance of rapid prototyping
Build Early, Build Often
Large, complex products seem incredibly difficult to model. That’s why many companies wait until late in the design cycle to start looking at a physical representation that people can see, feel, or otherwise use to simulate actual work.
Unfortunately, by that late phase, usability challenges or other potential issues will be embedded in the design. You’ll have also already invested a lot of time, money, and energy. The larger and more complex the product, the more difficult and costly it is to change course once the design process is in motion.
In other words, these products’ size and complexity are precisely why you should build something early. That way, you’ll evaluate human factors and uncover potential usability issues before they become big problems. The sooner you can assess things that you need to experience, the fewer cost overruns, wasted hours, and stress you’ll have later.
When it comes to large equipment, it’s important to begin rapid prototyping as early as possible. Even a simple mock-up representing users’ basic interactions with the object enables you to literally see and feel potential design issues.
Pound for pound, physical mock-ups are the most valuable models you can make. Basic, inexpensive materials like cardboard or wood assembled quickly can provide immediate tactile feedback. And this rapid prototyping lets you build on what you learn before you start your prototype.
A prototype is the first functional version of your product when everything has been figured out and you can start reproducing its functional form. A “mock-up is a rudimentary, non-functional model built at an early stage that approximates the product’s size, touchpoints, and other aspects.
Don’t Let Software Fool You
3D CAD has become the common language of form creation in modern design and engineering. But its ability to quickly focus on the smallest details can also be a trap. The software can be deceiving when it comes to scale and other factors.
CAD won’t let you physically interact with the product, and interacting with a product is key to realizing if people can use it in real life. As this company learned, a CAD model is no substitute for a physical representation.
Even the most sophisticated imaging software (like AR and VR) will never show you every aspect of the actual device, and it doesn’t let you interact physically with the machine. Even engineers working closely with CAD outlines often end up surprised when they see the real thing at full size. That brings me to our next lesson learned.
Seeing Past Your Own Perspective
The team on the chip tester had produced a lot of similar devices. But even with all their experience and insight, these engineers needed the objective perspective of a physical object to see past their subjective experience.
A mock-up invites perspectives and input from others, which can provide a healthy challenge to a particular point of view. Seeing and touching the cube allowed this team to pause and consider what the experience might be like for a wider range of people. It’s hard to argue for a particular design when a colleague cannot use it.
Big Machines for Human-Sized Work
Big machines are usually based on big, sophisticated technology. But ultimately, big machines exist just to support people solving big problems. So, they should become a seamless extension of their work. But the interaction between people and big equipment is complicated and difficult to imagine on paper or through software.
Understanding the literal act of that work through physical prototyping helps ensure that connection. It also avoids costly disappointments once the product is used in the lab or on the factory floor.
Design is crucial, so when should you start considering it? As this company learned, the sooner, the better! In the next blog post in our series, we’ll explore why integrating design with engineering at the concept stage is critical to a product’s success.